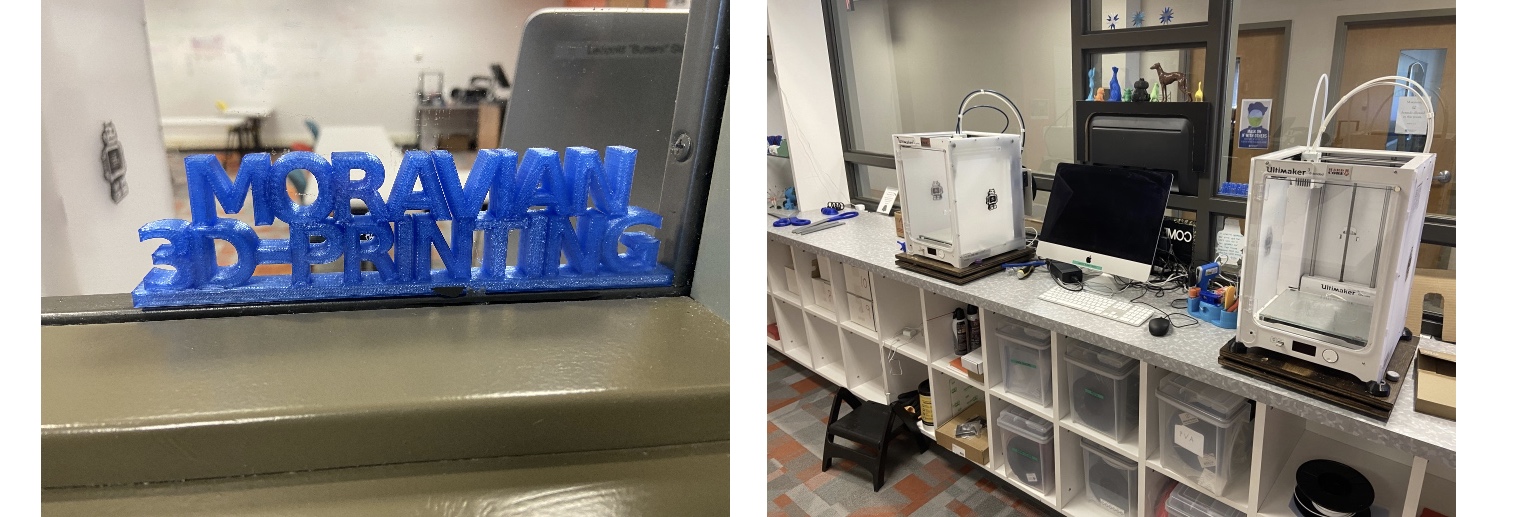
By Jeff Dickens
The ribbon cutting ceremony for the Debra Gaspar Reading Nook was fast approaching — April 19 — and no scissors to cut the ribbon! What to do? Janet Ohles, director of Reeves Library and organizer of the event, remembered the 3D printing lab located in the Priscilla Payne Hurd Academic Complex. She contacted Jeff Bush in the Computer Science department for help. Could a ceremonial pair of scissors be produced in time for the event? In three days? Why, yes.
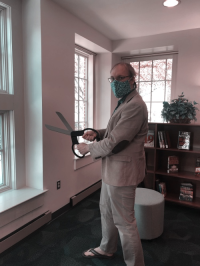
This is the magic of 3D printing. With raw plastic (and occasionally other materials, like Bronze!), some Computer Aided Design (CAD) programming skills, and a 3D printer, just about any object, including functioning objects with moving parts, can be made. Jeff handed the scissors project off to his student, Nikolas Kovacs. Nik found a prototype on the internet to work from, as there are many pre-programmed objects out there ready to download and print. This project, however, required some design intervention. The scissors were not big enough for ceremonial purposes, so Nik made some changes to the design, upscaled the size as much as the printers could handle, and after three iterations of printing, the final product: those giant scissors you see in the photo above.
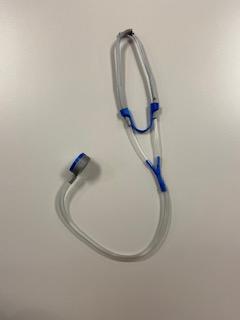
Jeff, whose PhD is in Computational Neuroscience, and his students make 3D objects for free, to anyone on campus who needs them for academics, facilities, and other purposes. At the outset of the pandemic, they made 500 functioning stethoscopes for St. Luke’s Hospital by working 24/7 in 6-hour shifts (!), with all ten printers in the lab working, an all-in-all impressive accomplishment (See here, here, and here). For the School of Nursing, students made plastic finger sleeves that hold Gatorade so nursing students can practice finger pricking for blood samples without having to, well, you know, prick real fingers. The finger sleeves are one of the projects that pose special challenges for 3D printing, as they require being made of soft plastic – hard plastic, by contrast, is much easier to work with, and is used to make most of the projects.
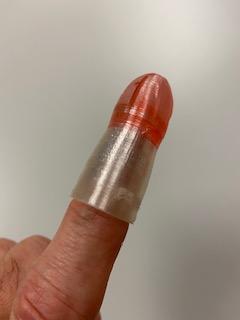
Jeff showed me around the lab to look at some of the projects spread out on the tables and cabinets. He showed me a Moravian hound made out of 80% bronze, and 20% plastic, made with a 3D printer. One project involved making a needle for an antique record player. Another project involved creating a weighted dice for the statistics department, so students can practice determining fairness by analyzing outcomes of dice rolls compared to unweighted dice. It works well for work-study students, too, who punch the clock to work on requested projects that require design input. Not all projects result in functional objects. At one point, the 3D printing club used the space to make little animal sculptures.
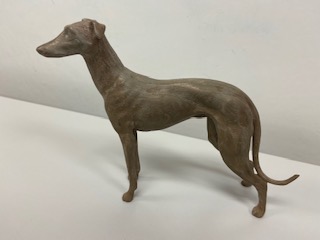
The possibilities endless? Maybe not, but they sure are extensive. It should be noted that the real ceremonial scissors did show up on time after all. It is also true that, as it turns out, these printed 3D scissors were designed to cut crepe paper that the designers were told would be purchased for the event — the addition of metal blades would have been attached for cutting ribbon. Nonetheless, what lesson was learned? The next time you need a 3D object that seems unreachable, think of the 3D printing lab in the Priscilla Payne Hurd Academic Complex. The success of 3D printing on campus speaks for itself.
3D Printing Lab:
Email: 3d@moravian.edu.
Website: 3d.moravian.edu.